Warehouse operations are the backbone of supply chains, yet many managers face persistent challenges in maintaining efficiency. Issues like inventory inaccuracies, labor inefficiencies, and space constraints can hinder performance.
A study by Ken Research highlights that the Philippines’ warehousing market is projected to grow at a CAGR of 6.5% from 2023 to 2030, indicating a rising demand for efficient warehouse operations.
To navigate these challenges, it’s essential to explore solutions that enhance operational efficiency. This article delves into effective strategies and software solutions to optimize warehouse operations.
Table of Contents
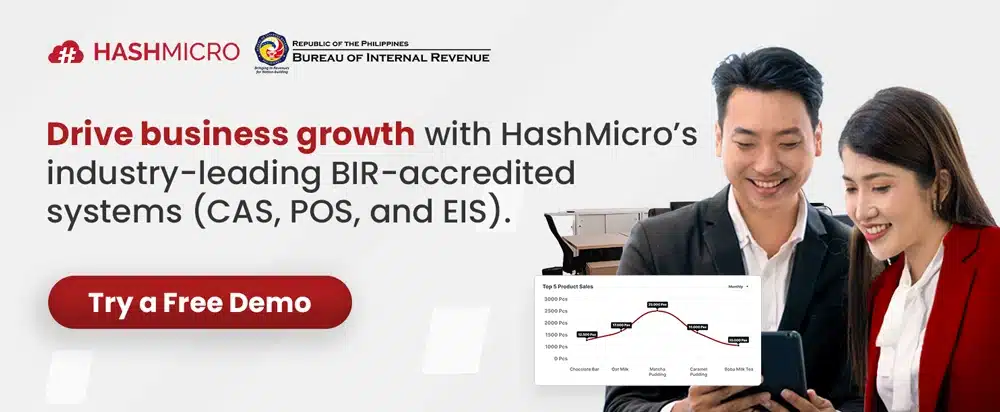
Key Takeaways
|
What is Warehouse Operations?
Warehouse operations are crucial for ensuring that goods flow smoothly in and out of a warehouse. These operations encompass a range of critical processes, including the receiving of goods, cross-docking, organizing and storing inventory, and the integration of asset tracking solutions like barcodes to monitor inventory efficiently.
To maintain streamlined operations, it’s important to focus on managing every step in the warehouse process, from selecting picking routes and establishing sorting and packing practices to maintaining the warehouse facility. Effective warehouse management also involves overseeing the integration of new technology, including the selection and maintenance of a WMS to enhance overall productivity and accuracy.
In addition, warehouse operations management extends to optimizing the racking designs, warehouse infrastructure, and ensuring smooth distribution to customers. With the rise of e-commerce and heightened customer expectations, businesses must refine their operations to stay competitive, maximizing efficiency while maintaining high customer satisfaction and profitability.
What are the Key Work Activities in Warehouse Operations?
Efficient warehouse operations are critical to the smooth functioning of any supply chain. By understanding and optimizing each step, from receiving goods to shipping them out, businesses can significantly improve their operational efficiency.
The following key activities highlight the core processes involved in warehouse operations management that contribute to streamlined workflows and timely deliveries.
- Receiving: This is the initial step where incoming goods are received, inspected, and labeled. It ensures that products meet quality standards and are accurately recorded before entering the warehouse operations system.
- Put-away: After receiving goods, they are placed in the appropriate storage area. This process is crucial for maintaining an organized warehouse and ensures that items are easy to retrieve when needed.
- Storage: Efficient storage involves organizing goods in a way that maximizes space and optimizes workflow. Warehouse operation management focuses on ensuring that the storage area supports smooth, quick, and error-free processes.
- Picking: Picking refers to selecting the right items for orders, either manually or using automation. This step is essential in fulfilling both B2B orders and direct-to-consumer shipments accurately and on time.
- Packing: After picking, items are securely packed in boxes, ensuring minimal empty space. Proper packing is vital to prevent damage and maximize shipping efficiency, a key part of basic warehouse operations.
- Shipping: The final step in warehouse operations is shipping, where packed orders are handed over to the transport company. This process includes verifying the order before dispatch to ensure that customers receive the correct products on time.
By effectively managing these activities, businesses can ensure their warehouse operations run smoothly, improving efficiency and customer satisfaction.
Warehouse Operations Jobs & Responsibilities
In warehouse operations, having clear job roles and responsibilities is essential to ensuring the smooth running of the entire process. From managing staffing levels to overseeing daily activities, each role contributes to the overall efficiency and success of the warehouse.
The right software can play a pivotal role in supporting these jobs, helping streamline workflows, improve accuracy, and ultimately enhance productivity across all areas.
1. Warehouse operations manager
The Warehouse Operations Manager oversees the day-to-day activities of the warehouse, ensuring that all operations run smoothly and efficiently. They are responsible for managing workflows, resolving operational challenges, and maintaining safety protocols.
In addition, they handle staff management, including training, scheduling, and performance reviews. Using the right warehouse management software can streamline these tasks, providing real-time insights and facilitating better decision-making across operations.
2. Warehouse supervisor
A Warehouse Supervisor manages teams of workers and ensures that they complete tasks on time and according to company standards. They supervise warehouse activities, coordinate shifts, and ensure compliance with health and safety regulations.
Additionally, they may provide on-the-job training to new employees. Leveraging warehouse operation management software can improve task allocation, track performance, and ensure that supervisors can efficiently monitor multiple warehouses.
3. Warehouse clerk
Warehouse Clerks are responsible for organizing and managing inventory within the warehouse, ensuring goods are received, stored, and prepared for shipment. They maintain accurate records of inventory, assist with order fulfillment, and coordinate with other staff to ensure smooth operations.
A robust warehouse management system (WMS) can automate inventory tracking, making the clerk’s role more efficient and less prone to human error, ultimately improving overall warehouse operations.
4. Warehouse worker
Warehouse Workers perform physical tasks such as loading and unloading shipments, moving goods within the facility, and maintaining the organization of storage areas. They may also operate equipment like forklifts or pallet jacks and help with inventory counts.
For large operations, using automated systems can reduce the physical strain on workers, optimize task allocation, and improve efficiency in the warehouse. Warehouse operations management software plays a key role in coordinating these tasks seamlessly across the workforce.
5. Staffing and resource management
Staffing in warehouse operations involves determining the right number and mix of employees based on workload demands. Effective staffing is essential for meeting operational goals without overspending on labor costs.
Calculating labor expenses and optimizing staffing levels through warehouse operations management software ensures that businesses can allocate resources efficiently, improving productivity and reducing unnecessary costs.
Warehouse Operations Processes & Workflows
Warehouse operations are a combination of processes and workflows designed to ensure that goods are efficiently received, stored, picked, and shipped to customers
Below, we’ll explore the key activities and workflows that are integral to successful warehouse operations:
1. Receiving
The receiving process involves checking incoming goods, verifying them against purchase orders (POs), and ensuring that all items meet quality standards. This step is crucial for maintaining accurate records and ensuring that the products are suitable for storage or immediate use in the warehouse operations.
Proper documentation, such as purchase orders and warehouse lease agreements, helps to maintain accountability and avoid errors during this phase. A well-organized receiving process sets the foundation for smooth warehouse operation management and efficient inventory control.
2. Storing
Once goods are received, they need to be stored in appropriate areas until needed for packing or shipping. Warehouse storage areas vary depending on the product, such as cold storage for perishable goods or palletized racks for bulk items.
Efficient storage is key to maximizing warehouse space, and methods like pallet racking systems or film wrap machines for delicate items help protect products. Proper storage management ensures that inventory is easily accessible, helping streamline basic warehouse operations.
3. Picking
Picking involves selecting items from storage to fulfill customer orders, which can be done manually or with automation. Different picking systems, like gravity-fed conveyors or robotic vehicles, can speed up the process and reduce human error.
Whether it’s for a business-to-business (B2B) or direct-to-consumer order, the picking process must be precise to ensure correct items are selected. Warehouse operations management tools can optimize picking workflows, improving accuracy and speed in fulfilling orders.
4. Returns
Managing returns efficiently is essential in warehouse operations, as products may be returned for reasons like defects or incorrect orders. This process includes receiving the returns, inspecting them for damage, and classifying them based on their condition (e.g., resalable, repairable, or scrap).
Well-documented returns management systems (RMS) track and process returned items to minimize losses and improve customer satisfaction. Implementing a returns process is crucial for optimizing inventory levels and maintaining smooth warehouse operations.
5. Data collection and analysis
Collecting and analyzing warehouse data, including inventory, orders, labor, and equipment usage, is vital for optimizing warehouse operations. By monitoring key performance indicators (KPIs), warehouse managers can identify areas for improvement, reduce costs, and increase productivity.
Warehouse operation management software can automate data collection, making it easier to track inventory levels, labor efficiency, and equipment utilization. Leveraging data-driven insights allows businesses to refine their operations and continuously improve efficiency.
5 Ways to Improve Warehouse Operations Efficiency
To enhance warehouse operations, it’s essential to focus on improving efficiency across various processes. Small improvements in key areas can have a significant impact on overall performance and cost-effectiveness.
Here are five effective strategies to boost warehouse operations efficiency and streamline workflows:
1. Implementing a Warehouse Management System (WMS)
A Warehouse Management System (WMS) is a powerful tool that optimizes the flow of goods and materials throughout the warehouse. By automating key tasks such as receiving, putaway, picking, packing, and shipping, a WMS ensures that operations are streamlined and efficient.
It also provides real-time insights into inventory levels, orders, and labor productivity, enabling warehouse managers to make data-driven decisions. With a robust WMS in place, warehouse operations management becomes more precise and effective, reducing errors and enhancing overall performance.
2. Streamlining the layout and design of the warehouse
The layout and design of your warehouse can significantly impact efficiency. By strategically grouping similar products together and placing frequently used items closer to the packing and shipping areas, you reduce unnecessary movement.
An optimized warehouse layout minimizes travel time, ensuring that goods are moved quickly and efficiently from one point to another. This small but impactful change helps ensure smooth material flow, making basic warehouse operations more streamlined and cost-effective.
3. Improving the accuracy and speed of order picking
Order picking is one of the most time-consuming tasks in warehouse operations, and improving its accuracy and speed can have a major impact on overall efficiency. By implementing technologies such as pick-to-light systems and barcode scanners, you can minimize errors and speed up the picking process.
Additionally, creating efficient picking routes helps workers select the correct items faster, further reducing time spent on this task. With faster and more accurate order picking, warehouse operation management becomes far more effective, ensuring that orders are fulfilled quickly and accurately.
4. Optimizing inventory levels
Maintaining the right balance of inventory is crucial to warehouse efficiency. Too much inventory can lead to overstock and wasted space, while too little can cause stockouts and delays.
Implementing methods such as Just-in-Time (JIT) inventory, using safety stock for unforeseen demand, and employing perpetual inventory systems can ensure inventory levels are optimized. Real-time inventory tracking enables warehouse operations to be more responsive and agile, preventing disruptions and improving the flow of goods.
5. Automating tasks
Automation is a game-changer in warehouse operations, helping to speed up processes and reduce manual labor. Technologies such as conveyor belts, robotic arms, and Automated Storage and Retrieval Systems (ASRS) can automate key tasks such as receiving, putaway, order picking, and shipping.
Automation reduces human error, minimizes the time spent on repetitive tasks, and increases throughput. By incorporating automation into warehouse operations, businesses can significantly boost efficiency and streamline their entire operation.
By focusing on these key areas, businesses can enhance their warehouse operations management, reduce inefficiencies, and ensure smoother, more productive processes.
Boost Operational Efficiency in Your Business with HashMicro Warehouse Management Software
Struggling to keep your warehouse operations organized and efficient? HashMicro’s Warehouse Management System (WMS) helps businesses in the Philippines take control of their operations, improving inventory management, streamlining workflows, and enhancing overall efficiency.
By using HashMicro’s WMS, you gain real-time visibility into every aspect of your warehouse, from inventory tracking to order fulfillment and shipping. This allows you to monitor performance and make data-driven decisions, ensuring smooth operations even during peak periods.
Our in-depth analytics provide insights into inventory patterns and workflow bottlenecks, enabling you to reduce delays, minimize errors, and optimize processes without compromising quality.
The following are the main features of the HashMicro WMS:
- Inventory Forecasting: This feature uses historical data, trends, and seasonal patterns to predict future inventory needs, ensuring optimal stock levels. By keeping inventory balanced, businesses can avoid stockouts and overstocking, enhancing operational efficiency.
- Goods Management by Category & Storage Method: The system categorizes goods based on dimensions, type, and storage method, like FIFO or FEFO, and links items to suppliers. This ensures systematic and accurate tracking, improving the procurement process and minimizing errors in inventory handling.
- Multi Warehouse & Locations: The software efficiently manages inventory across multiple warehouses and locations, ensuring balanced distribution. By preventing stock imbalances, businesses can optimize storage and improve delivery times across all their operations.
- Run-Rate Tracking: By monitoring stock consumption rates in real-time, this feature helps predict when to reorder supplies, preventing stockouts. This proactive approach improves inventory planning, ensuring that stock is always available without unnecessary overstocking.
- RFID (Radio Frequency Identification): RFID technology automates item tracking, increasing accuracy and speed in warehouse management. This boosts operational efficiency by reducing human errors and accelerating inventory handling processes.
- Stock Request Management: This feature manages internal stock requests between departments or locations, ensuring efficient stock allocation. By streamlining this process, businesses can ensure that stock is distributed where it’s needed most, reducing wastage and delays.
- Barcode Management: The system tracks inventory using barcodes, improving stock accuracy and reducing errors in stock levels. This efficient tracking helps maintain accurate records, preventing discrepancies and optimizing inventory control.
- Stock In & Out: This feature tracks all stock movements, both incoming and outgoing, and provides real-time stock data. By having complete visibility of stock flows, businesses can improve inventory tracking, reduce losses, and streamline supply chain operations.
With HashMicro’s WMS, managing your warehouse becomes more efficient and effective. Our powerful tools help you improve inventory accuracy, reduce processing times, and maximize profitability by ensuring seamless operations and faster fulfillment.
Conclusion
Warehouse operations are crucial to the smooth functioning of supply chains, involving processes like receiving, storing, picking, and shipping goods. Efficient warehouse operations lead to reduced costs, improved customer satisfaction, and better overall productivity.
By implementing HashMicro’s Warehouse Management System (WMS), businesses can optimize these key processes with real-time visibility and automation. Our WMS streamlines inventory management, order fulfillment, and shipping, helping businesses improve efficiency and reduce human error, ultimately enhancing profitability.
Experience the benefits of streamlined warehouse operations firsthand by trying out HashMicro’s WMS with a free demo. Our team is ready to show you how our software can transform your operations and boost your business’s efficiency.